Tile Machinery Inf.
Flowchart
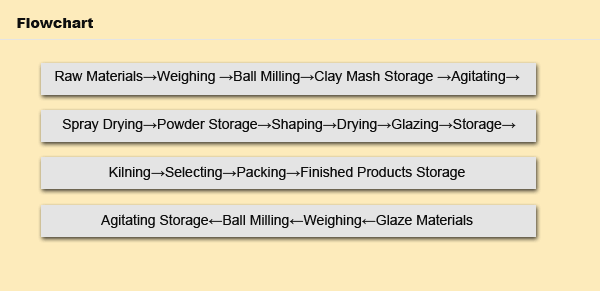
 Process description
1 Raw Materials Weighing:
The raw materials for single process type of ground ceramic tile, including various clays, feldspar and frit, are processed homogeneously by mixing and ball milling. All the raw materials should be accurately weighed, so that the quality of the product can be stabilized. It is therefore essential that precision weighing equipment be prepared. Roof tile making machine.
2 Ball Milling:
After weighing, the raw materials are transferred to the ball mill, where water is added. After crushing and agitating, the clay is forced to pass through a 80-100 mesh screen in order to make into delicate products.
Nowadays, the ball mill is lined with oxidized aluminum, which is more efficient and can save 1/3 of time.
3 Mixing:
Making the ingredients of the clay well-distributed in the solution, and keep it from sedimentation, which is good for forming. Roof tile making machine.
4 Vibrating screening:
Vibrating screen is placed at the outlet of ball mill, refraining the coarse particle materials from flowing through the 80-100 mesh screen down to the ground tanks. Roof tile making machine.
5 Spray Drying:
The most modernized and efficient method for making body slip is by spray drying powder method. The powder formed is round shape, and ball. The size of granules can be adjustable depending on the demand of the users. After spray drying, the water content of the granules is between 35-40%.
6 Powder Storage:
The granules have to be kept in a storage bin for a few days so that its composition becomes even more homogeneous. This process makes the granules more pliable and less likely to stick to the mold. The size of powder storage bin needed will be determined by the production capacity of the plant. Generally, the most suitable size is capable of holding 400 tons of powder. Roof tile making machine.
7 Shaping:
After storage, the granules is conveyed to a shaping machine and to be molded by squeezed with high pressure into what is called a biscuit. Roof tile making machine.
8 Speed Body Drying:
The water content ranges between 6-6.5% after squashed. The biscuit is then conveyed through the speed drying kiln to lower the water content to below 1%, and to be ready for firing in the kiln. Roof tile making machine.
9 Glazing:
The dried biscuit to be put on raw-body glazing lines and sprayed with glaze on the surface, the different glazes, after firing, will turn out different colors. After the biscuit is glazed, it can be embossed and printed with various designs and colors by different glazing process. Roof tile making machine.
10 Car Storage:
After glazing, the biscuit is loaded into the stock car for storage, which is proceeded by the fully-automatic hydraulic controlled system. Roof tile making machine.
11 Speed Rolling Kiln Firing:
The biscuit is conveyed along the high speed rolling kiln and heated with a temperature of 1,150-1,200oC.
12 Selecting:
At the outlet of the kiln, the defective products will be selected out. Roof tile making machine.
13 Packing:
The finished products are then packed and stored or shipped. Roof tile making machine.